- FMA
- The Fabricator
- FABTECH
- Canadian Metalworking
Fabricating/press brakes
- February 2, 2010
- Product Release
- Metalworking
Cincinnati Inc. brings easy-to-use PC-based control to shops of all sizes with its affordable new Proform hydraulic press brake.
The control combines 3D graphics interface with simple touch-screen operation to speed setup and programming times, as well as optimize throughput. Precision servo hydraulics on a proven, rigid press brake platform allow the Proform to hold ram repeatability to ±0.001 in. (0.025 mm) along its entire length.
The press brake is available in 60 to 350 ton versions in overall bed lengths from 4 to 14 ft., and offers a wide variety of options to best match press brake to process. The LCD touch-screen control uses simple icon-driven Windows operating system, eliminating the need for keypads and key switches. Advanced control software allows helpful 3D rotational viewing of the part, detailing part shape and gage fingers.
New part programs can be generated through manual data entry or by drawing the part in cross-section or flat pattern, and then selecting tooling and bend sequence. A special job setup page displays tool segment lengths and tool locations, as well as notes to reduce setup time. The control can access jobs from its internal hard drive, floppy disk or network connection.
Cincinnati has integrated a number of its proven press brake design principles for reliable, long-lived operation:
•clevis-mounted cylinders and centerline loading that confine operating stress within the main housing to eliminate cylinder misalignment;
•Variable Volume Load Sensing (VVLS) hydraulic system for lower maintenance costs and greater energy efficiency;
•hardened piston rods with precision guiding to eliminate cylinder oil leaks; •rigid interlock construction for maximum durability; and
•precision-engineered Microcrown machined into the press beds of 90- to 350-ton versions to reduce die shimming.
Absolute linear transducers mounted on both ends of the machine provide automatic leveling control by maintaining parallelism between the bed and ram. The transducers are referenced below the neutral axis of the throat to avoid ram reversal errors due to side housing deflection. Each press brake is tested before shipping to ensure ram repeatability to ±0.001" (±3 sigma). Adjustable stroke length and full-tonnage throughout the stroke.
Designed for application versatility, the Proform is available with a variety of tool holders, filler blocks, and ram noses to accommodate most major tooling types, including US or European-style tooling. Fast tool change systems are available with European tooling, and a European-style bolt-on ram nose is a no-cost option on 60-ton models. Optional AUTO CROWN automatically produces an upward force on the bed proportional to the ram force to deliver consistent bends along the entire bend line
Other options include power clamp, hardened wear strip, presence sensing, fluid monitoring, heater units and heat exchangers. Numerous CNC backgage configurations are available from one to four axes for sheet and plate applications.
subscribe now
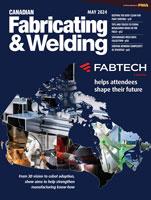
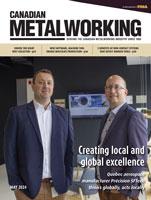
Keep up to date with the latest news, events, and technology for all things metal from our pair of monthly magazines written specifically for Canadian manufacturers!
Start Your Free Subscription- Industry Events
MME Saskatoon
- May 28, 2024
- Saskatoon, SK Canada
CME's Health & Safety Symposium for Manufacturers
- May 29, 2024
- Mississauga, ON Canada
DiPaolo Machine Tools Open House 2024
- June 4 - 5, 2024
- Mississauga, ON Canada
FABTECH Canada
- June 11 - 13, 2024
- Toronto, ON Canada
Zoller Open House & Technology Days 2024
- June 12 - 13, 2024
- Ann Arbor, MI