product marketing manager
- FMA
- The Fabricator
- FABTECH
- Canadian Metalworking
Achieving success with mechanized plasma cutting
Best practices to produce better cuts
- By Jorge Santana
- April 22, 2024
- Article
- Fabricating
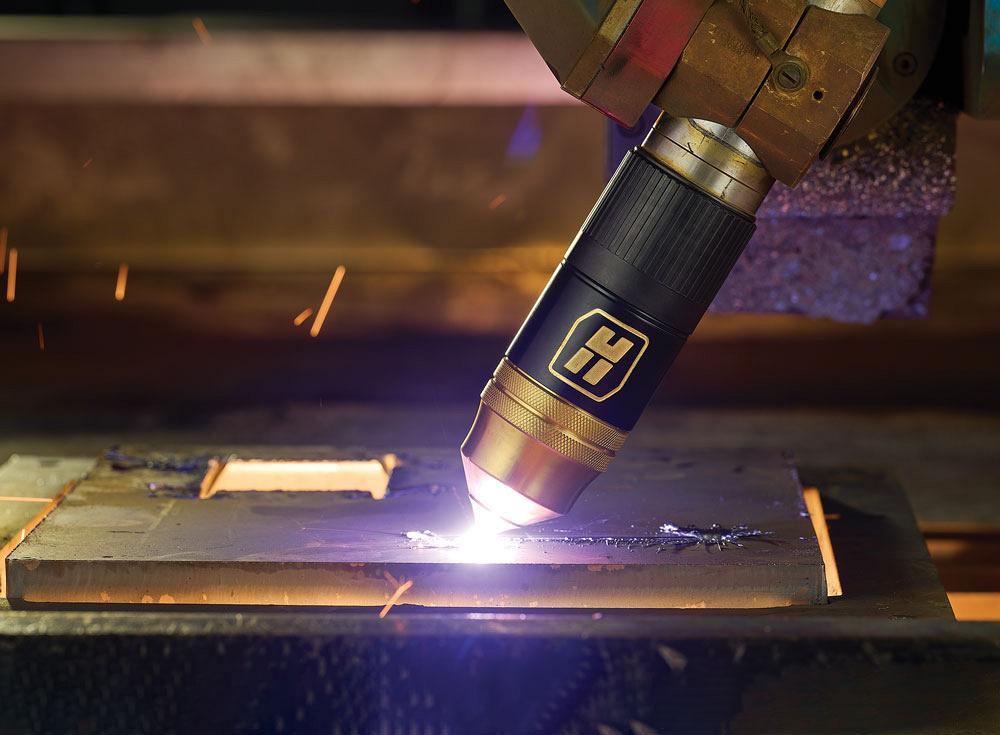
Operators will sometimes install consumables in the wrong order. Hypertherm HPR cartridges replace five standard consumables, eliminating costly stack-up errors.
There are many different metal cutting methods available today, and each has its own benefits and caveats. Mechanized plasma is a very versatile, productive, and highly adaptable way to cut metals in multiple applications and at a relatively low cost of acquisition.
The technology is mature, and many fabricators have experience working with plasma or have at least some familiarity with the process and its parameters. For this reason, mechanize plasma often requires less training than other processes. Also, technicians and operators tend to find plasma to be friendlier to service because of their understanding of and familiarity with the process.
Even though every system architecture is unique and every consumable is different, it is important to understand the features and function of each part.
While the technology is a great starting point for new operators, knowing some basic best practices involving the cutting table, CNC settings, and consumables will help you ensure that plasma cutting runs smoothly and efficiently.
Cutting Table
The cutting table is one of the first things to visually inspect before beginning a plasma cutting operation.
Ensure Slats Are Clean. The slats on a cutting table will require periodic cleaning, especially after cutting lots of plate. The frequency of cleaning will depend on the amount of dross buildup on the slats. Any debris on the slats can cause the plate to rest unevenly, which directly affects the torch height and cut angle, possibly resulting in blowbacks, double arcing, and ramp-down errors.
CNC Settings
For the most part, all necessary cutting information is saved on the CNC. For instance, if you are about to cut a specific part and are setting up that part program, the CNC will identify the consumables that are supposed to be used and include a photo or visual representation.
While modern CNCs have multiple built-in tools that require minimal operator intervention, there are variables that you should keep in mind to ensure optimum cutting outcomes.
Ensure Proper Gas Flow and Pressure. Changes in gas flow, gas pressure, or amperage will cause the plasma arc characteristics to change, which can negatively affect consumable life and cut quality. If pressure is too low, the plasma arc will not form correctly, leading to poor cut quality and excessive dross. If the pressure is too high, it will affect the concentrated arc column, which will disperse the energy of the arc causing poor cut quality.
Be sure to refer to the manufacturer’s user manual to determine the proper cut-flow gas settings for various processes. You also should check gas flow and pressure levels every day to ensure the correct amount of gas is reaching the plasma torch. When cutting with air as a shielding gas, it is equally important is to ensure that the air is dry and clean (oil free). Contaminated air can cause low consumable life and cut quality issues.
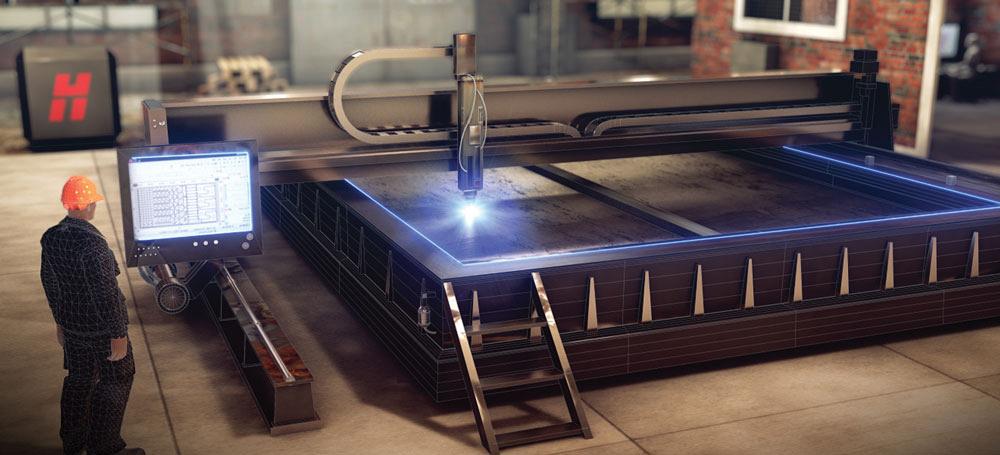
Performing a visual inspection on consumable components and replacing parts regularly is a great start.
Also, if a compressor is constantly running to keep up with the plasma, this can generate heat and moisture inside the tank that flows into the air lines and then into the torch and consumables. This could be an indication that your air compressor is undersized for your application.
Ensure Proper Torch Height. Plasma cutting has two different torch control height settings: pierce height and cut height.
With automated plasma cutting, the torch must be separated from the plate to ensure optimal performance, decrease heath exposure [exposure to unsafe fumes], and avoid torch collisions with the plate. If the pierce height is set too low, the torch will be too close to the plate while piercing, which can lead to the molten metal spraying back to the torch and damaging the consumables. If it is too high, the arc will not transfer, causing a misfire, which also can damage consumables.
Ensure that the proper pierce height, which is listed in the user’s manual, is programmed in your system’s torch height control (THC). If you are unable to verify this, a good rule of thumb is to move the torch away from the plate so it is one-and-a-half to two times the cut height.
Now, let’s look at cut height. Once your torch has pierced the plate and begun to cut, your THC will start to sample arc voltage from the power supply and compare it to the target voltage set in the CNC. It will then adjust the torch up or down to maintain that target voltage. Each voltage setting corresponds to a specific height that optimizes the arc characteristics for a clean, straight cut. If you set the voltage too high, the very tip—not the middle—of the arc will contact the plate. This will result in the removal of too much material from the top of the cut, which causes excessive top rounding and a positive bevel. Setting the voltage too low removes too much material from the bottom of the cut, leading to a negative bevel.
To avoid this error, ensure the arc voltage programmed into your THC follows the recommended cut height found in your operator’s manual. If you suspect your THC is not making the needed adjustments automatically, consider making adjustments manually.
Ensure Proper Plasma Process Selection for Your Application. Application-specific information makes all the difference. When cutting a specific material and thickness, it’s important to understand the appropriate process and consumables needed to be successful.
If you are cutting 0.5-in. mild steel plate and the process requires 170 amps, you can’t expect the best outcome if you run at 300 amps instead. That is not to say that different configurations can’t work, but the results may not always be optimal.
When in doubt, always consult the user’s manual.
Consumables
Nozzles, electrodes, and shields are usually replaced with regular frequency. The rest of the consumables, swirl rings, nozzle retaining caps, and shield caps, also should be replaced, albeit less frequently, to ensure the best cutting performance. Consult your user’s manual for more information about consumable changeover.
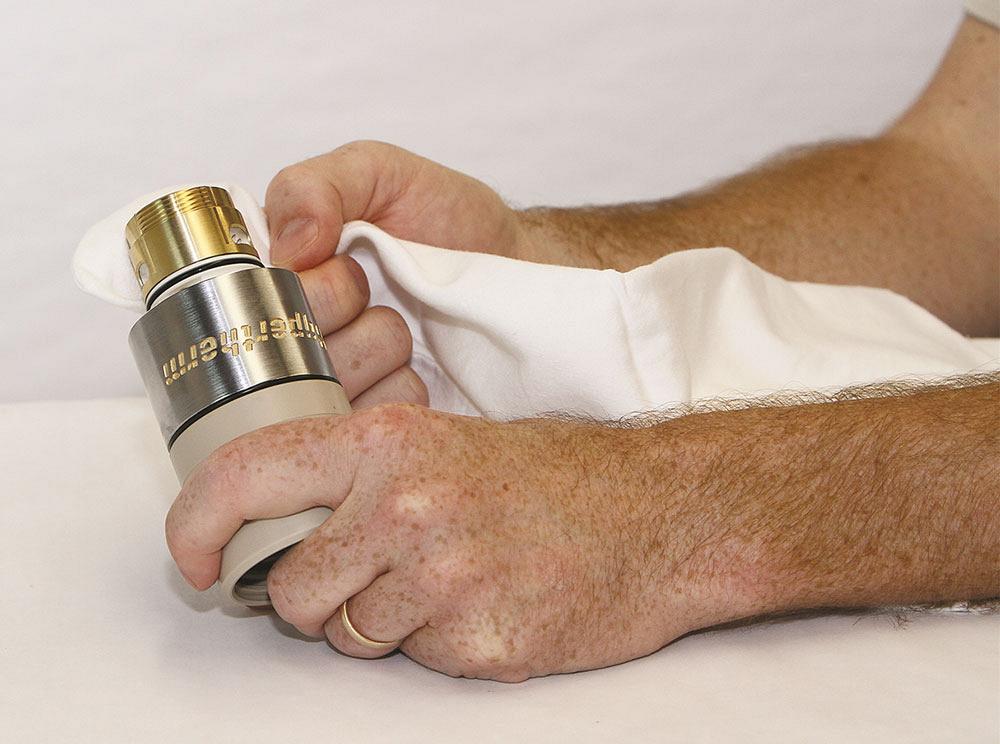
When changing parts, wash your hands and keep consumables on a clean shop rag to prevent contamination from dirt or metal dust.
Be sure to install the correct consumable set for the specific process you are using. Mixing parts will result in poor performance, system errors, and bad cutting outcomes.
One way to ensure you are using the correct consumables is to match the part numbers laser etched on each consumable part with the part number found in the manual.
Pro Tip: If you are cutting different material types and thicknesses regularly, keep backup torches preloaded with the correct consumables for the process rather than switching back and forth. This not only will help save time, but it also will prevent any mistakes in consumable selection.
Follow Preventive Maintenance Schedules. A preventive maintenance schedule based on both time and arc hours can help you monitor consumables properly. User’s manuals oftentimes include graphics that show when a nozzle needs to be changed or how an electrode looks when the hafnium or tungsten has been depleted.
Performing a visual inspection on consumable components and replacing parts regularly is a great start. Beyond that, having a schedule for changing out the coolant and filters will help keep the system running efficiently.
Verify the Torch’s Condition. It’s good practice to verify that the torch is in good condition to ensure that it lasts as long as possible. And while the torch will wear over time, accessories like an O-ring kit will help extend its life.
O-rings often can be a challenge for torch maintenance because hey require the right amount of lubricant. Too much lubricant will cause clogging and contamination in the torch. Too little, and it will be impossible to fit the O-ring in the torch, or it will crack, leak, or damage the torch. An O-ring should have just enough lubricant to make it look wet but without any physical buildup.
Jorge Santana is product marketing manager for heavy industrial plasma business at Hypertherm Associates, 21 Great Hollow Rd., Hanover, N.H. 03755, 603-643-3441, www.hypertherm.com.
About the Author
subscribe now
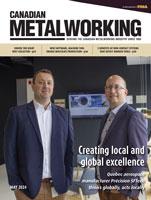
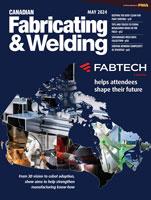
Keep up to date with the latest news, events, and technology for all things metal from our pair of monthly magazines written specifically for Canadian manufacturers!
Start Your Free Subscription- Industry Events
Automate 2024
- May 6 - 9, 2024
- Chicago, IL
ANCA Open House
- May 7 - 8, 2024
- Wixom, MI
17th annual Joint Open House
- May 8 - 9, 2024
- Oakville and Mississauga, ON Canada
MME Saskatoon
- May 28, 2024
- Saskatoon, SK Canada
CME's Health & Safety Symposium for Manufacturers
- May 29, 2024
- Mississauga, ON Canada