- FMA
- The Fabricator
- FABTECH
- Canadian Metalworking
Getting a Healthy Grip
Ergonomic designs make working with hand-held power tools less tiring, safer, and more profitable.
- By Sue Roberts
- May 13, 2016
- Article
- Fabricating
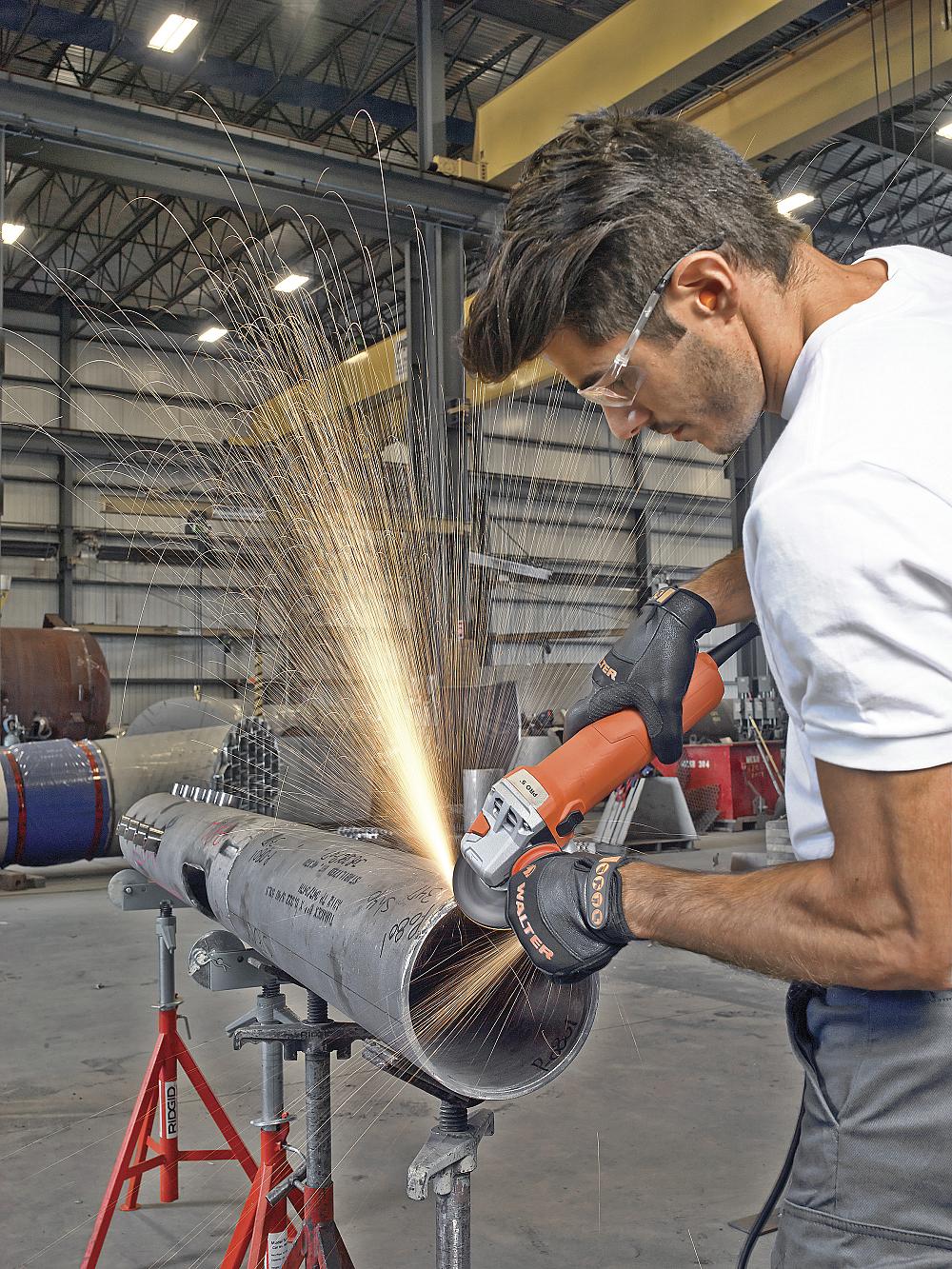
Small, versatile grinders with variable speed selectors can offer the same ergonomic features as the larger models and allow operators to choose optimal speeds for each application. Photo courtesy of Walter Surface Technologies.
Take a moment to look at your hands. Consider how they serve you. Think about their work on a metal assembly, grip on a golf club or hockey stick, or how they hold someone’s hand. Your sense of feel, or haptic perception, allows your brain to localize and evaluate touch, pressure, and temperature.
Using hand-held power tools that transmit vibrations, require wrists to bend to accomplish the task, or need frequent movements and pressure of the index finger to maintain operation can put your haptic perception at risk. Your ability to grasp and pick up items or feel sensation in your hands may be impaired and/or replaced with pain when making simple movements.
Hand-held power tools were involved in over 2,330 lost-time accidents across Canada in 2014, according to the Canadian Centre for Occupational Health and Safety. Unfortunately, the number of incidents remains fairly consistent from year to year. In 2012 there were 2,298; in 2013 there were 2,430.
Manufacturers of power angle grinders, angle or palm sanders, brushes, and right-angle drills continue to change equipment designs to make operation of these tools easier and safer. They have offered new handle configurations, lighter-weight tool casings with better insulating materials, features to reduce rotational vibration, and more power in smaller tools to make operation more ergonomically friendly for long-term use.
Discomfort Eased
Tasks like grinding, drilling, and hand finishing aren’t too physically taxing when they are interspersed between other activities. However, it is becoming more common to find individuals performing these kinds of tasks for the majority of their workday. Properly using tools designed to alleviate discomfort offers added protection against injuries, a reduction of overall physical fatigue, and more productivity.
John Thompson, national technical sales training manager for PFERD USA, said, “There have been significant changes to the design guidelines for power tools over the past 20 years. It really started with pistol-grip drills. Design modifications allowed the use of the inside cup of the thumb for support rather than transfer all the stress to the operator’s wrist.
“During this same period, many ergonomic changes occurred with the right-angle grinder. Right-angle grinders have gone from a simple barrel-style handle to a reduced-diameter, tail-style handle, nicknamed the ‘rat tail’ in the industry. The tailed handle helps reduce fatigue from holding the grinder for long periods of time, allows the use of gloves to reduce vibration and the potential for white-knuckle syndrome, and offers better operator control. With the added safety of a nonlocking switch and a vibration isolation second handle, the tail-style grinder is becoming more popular every day.”
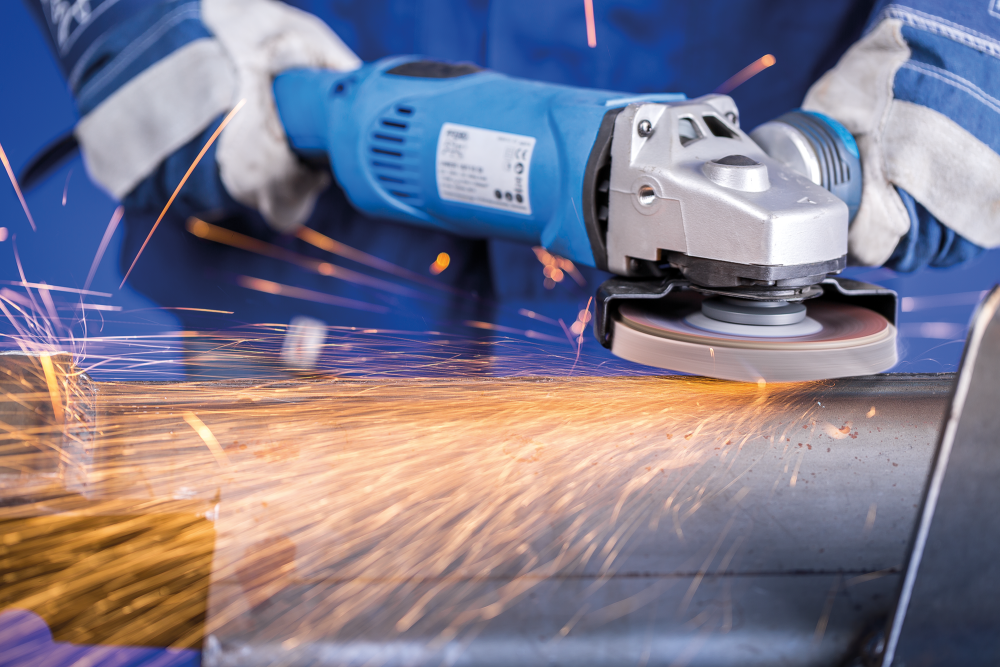
Match a hand-held power tool to the consumable product for the material and to the application to accomplish a task in the least amount of time with the least amount of human effort. Photo courtesy of PFERD USA.
Vibration Nearly Eliminated
Features built into the ergonomic hand-held equipment can reduce vibration by 95 per cent.
Stephane Drainville, international product manager-tooling and power tools at Walter Surface Technologies, recommended using high-efficiency power tools with safety features such as mechanical clutches, antivibration side handles, electronic revolution per minute (RPM) control monitoring, stabilizers, and mechanical brake systems.
“All these features significantly reduce vibrations while increasing safety and productivity up to 30 per cent. Many power tools combine these features with nonlocking paddle switch versions which are more comfortable to use compared to previous models,” Drainville said.
“When you are in a work zone with plenty of room, the tail version of a power tool will be more comfortable to use and reduce the risk of wrist problems caused by holding and manipulating the tool over a long period of time. These power tools are ergonomically designed to maximize productivity when an application is on a table or in an easy-to-reach area. “However, many small and medium workshops prefer small, versatile tools that are now almost as efficient as their larger counterparts.” Drainville added, “Most injuries come from poor, discouraged usage of these tools, such as using the tool with one hand or constantly overloading the tool, which drastically increases vibration and stress on the hand’s nerves.”
Human Effort Reduced
Once the proper power tool is selected, the best thing a person can do is to let the power and consumable product combination tool do the work at the optimal recommended tool speed instead of the maximum speed. The worst thing is to push into the job.
“When something isn’t working as desired, the human response is to push harder, to put more physical effort into the situation. That results in more impact to the body, more fatigue, and can cause a dangerous loss of control. Pushing on the tool during operation is especially dangerous when working in tight spaces or when there is an uneven weight distribution such as standing on a ladder. Leaning into the job will actually reduce tool performance because the added pressure will slow the RPM,” Thompson said.
The solution, he added, is to select the right tool and consumable for the application and the available space. “It’s a fast thought process but one that can lead to adjustments before starting the work that will get the job done faster and with less effort.”
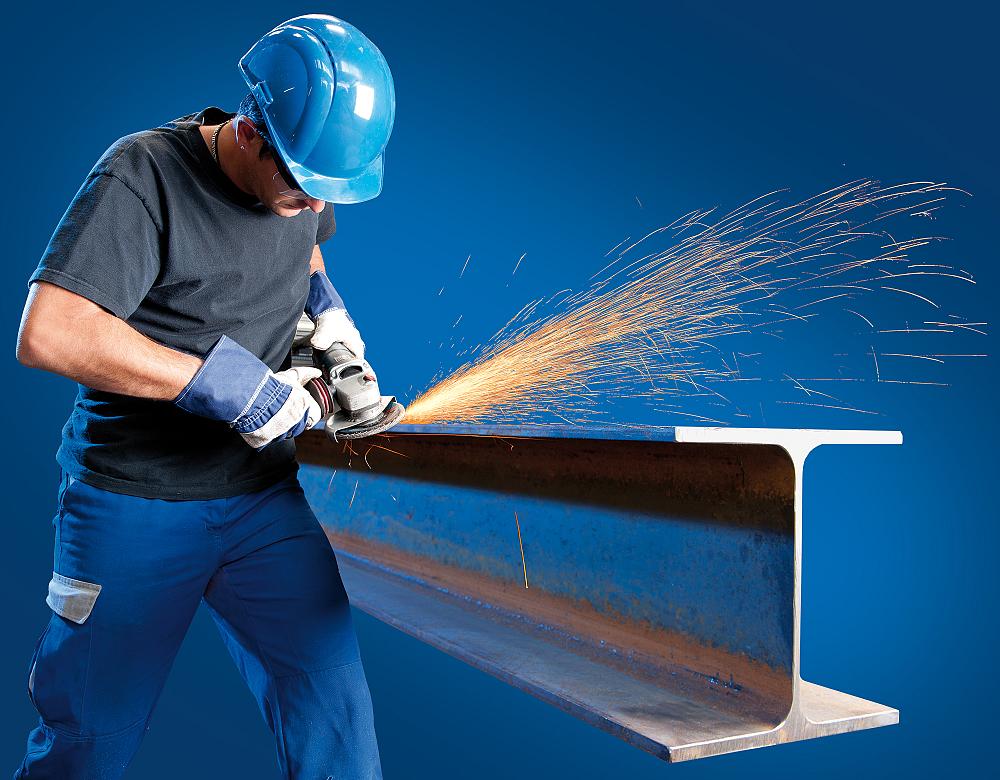
Let the power tool and consumable product combination do the work at the optimal recommended speed. Avoid leaning into the job, which reduces the tool’s RPMs and overall productivity. Photo courtesy of PFERD USA.
The focus on ergonomics has led to the development of many application-specific consumable products and equipment to meet different needs. For example, if a tight, narrow groove needs to be cleaned out, the tool of choice should have the power and speed to get the job done as quickly as possible while fitting in the work space with the least amount of twisting and turning of the wrist, arm, or body.
“Not all jobs require a one-off special tool. There is a lot of crossover,” said Thompson. “But it is important ergonomically--and on the production side--to match a hand-held power tool to the consumable product for the material and to the application. This will get the job done as quickly as possible with as little human effort and discomfort as possible.”
Investment Pays Off
“Ergonomically designed tools are more expensive, but the increased cost is very small compared to the productivity gain and human risk savings,” said Drainville. “In addition to the comfort, health, and safety advantages, productivity gains can easily return the cost of the tool in just a few working days. There is no cost savings when buying a cheap, unsafe hand-held power tool. It could take an hour to perform a task that can be done in 15 minutes when using a quality tool.”
Thompson said, “The more progressive shops look at their hand-held power tool investments in terms of risk reduction and overall minimizing the cost of doing business. Everybody could have new tools and consumables rather than paying for the cost of one injury. Often a shop will be ahead of the curve when new government regulations are enacted to protect workers.
“Literally spending a few more pennies on the correct hand-held power tool will reap dollars on the bottomline.”
6 Tips for Selecting a Hand-held Power Tool
Keep these tips from the Canadian Centre for Occupational Health and Safety in mind when you purchase a hand-held power tool:
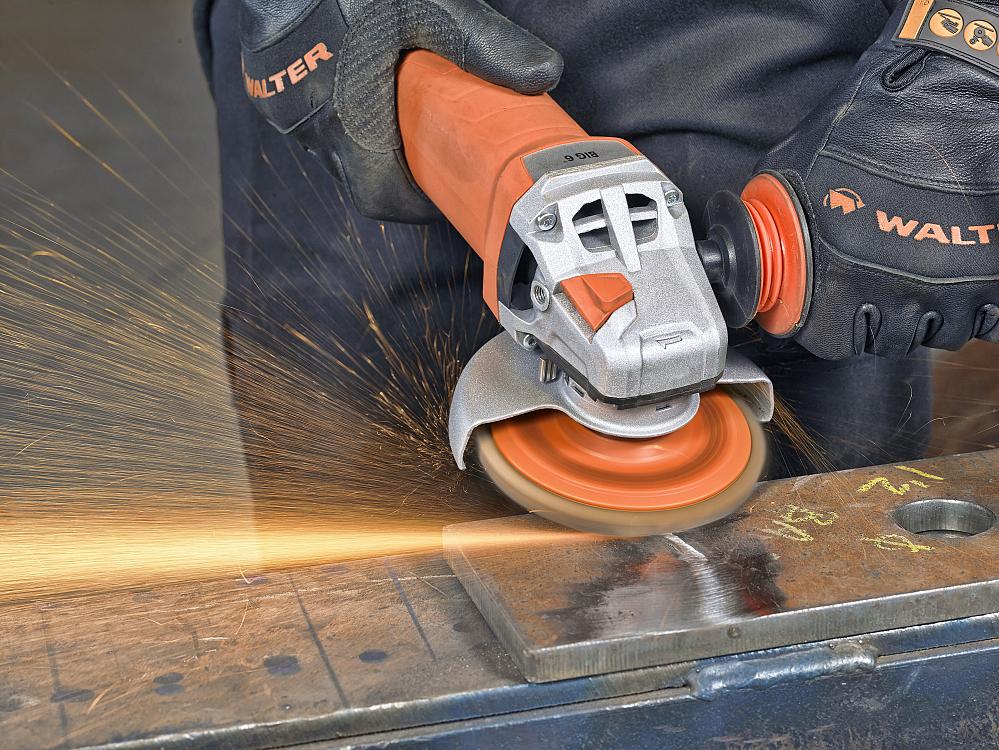
More power is being built into hand-held equipment to make long-term use less tiring. Photo courtesy of Walter Surface Technologies.
- Choose a tool that will allow the wrist to be straight during use. Bend the tool, not the wrist. Use tools with angled handles to work on hard-to-reach spots.
- Match the tool to the job. Consider the power needed to accomplish the job without exerting physical force, then choose the smallest, lightest-weight tool that will get the work done.
- Be sure the tool has vibration-dampening features.
- Look for rounded, smooth handles that provide a comfortable grip.
- Pick a tool with a double handle for easier holding and manipulation.
- Select a tool with a trigger strip that works easily rather than a button. A strip allows more energy to be exerted over a greater area to reduce muscle fatigue.
6 Tips for Using a Hand-held Power Tool
There are things you can do to reduce the ergonomic hazards of working with hand-held power tools. Here are six recommendations from the Canadian Centre for Occupational Health and Safety:
- Be sure the tool is in good repair.
- Hold the tool close to your body. Do not overreach.
- Keep good balance and proper footing to maintain control and manage unexpected situations.
- Use the lowest power setting available that will complete the job. This can reduce vibration.
- Rest your hands by putting the tool down when it is not in use.
- Wear antivibration gloves if the thick padding does not restrict any necessary movements.
Associate Editor Sue Roberts can be reached at sroberts@canadianfabweld.com.
PFERD USA, 262-443-4571, www.pferdusa.com
Walter Surface Technologies Inc., 888-592-5837, www.walter.com
About the Author
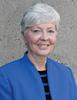
Sue Roberts
2135 Point Blvd
Elgin, IL 60123
815-227-8241
Sue Roberts, associate editor, contributes to both Canadian Metalworking and Canadian Fabricating & Welding. A metalworking industry veteran, she has contributed to marketing communications efforts and written B2B articles for the metal forming and fabricating, agriculture, food, financial, and regional tourism industries.
Roberts is a Northern Illinois University journalism graduate.
subscribe now
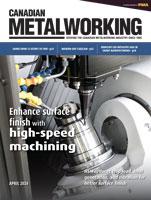
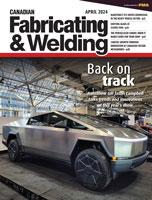
Keep up to date with the latest news, events, and technology for all things metal from our pair of monthly magazines written specifically for Canadian manufacturers!
Start Your Free Subscription- Trending Articles
Aluminum MIG welding wire upgraded with a proprietary and patented surface treatment technology
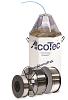
CWB Group launches full-cycle assessment and training program
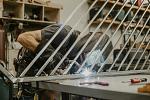
Achieving success with mechanized plasma cutting
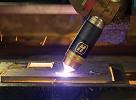
Hypertherm Associates partners with Rapyuta Robotics
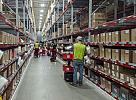
Brushless copper tubing cutter adjusts to ODs up to 2-1/8 in.
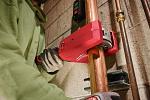
- Industry Events
MME Winnipeg
- April 30, 2024
- Winnipeg, ON Canada
CTMA Economic Uncertainty: Helping You Navigate Windsor Seminar
- April 30, 2024
- Windsor, ON Canada
CTMA Economic Uncertainty: Helping You Navigate Kitchener Seminar
- May 2, 2024
- Kitchener, ON Canada
Automate 2024
- May 6 - 9, 2024
- Chicago, IL
ANCA Open House
- May 7 - 8, 2024
- Wixom, MI