Associate Editor
- FMA
- The Fabricator
- FABTECH
- Canadian Metalworking
Toolholder considerations for working with large, heavy tools
Enabling features and following best practices will ensure process reliability
- By Lindsay Luminoso
- April 1, 2024
- Article
- Metalworking
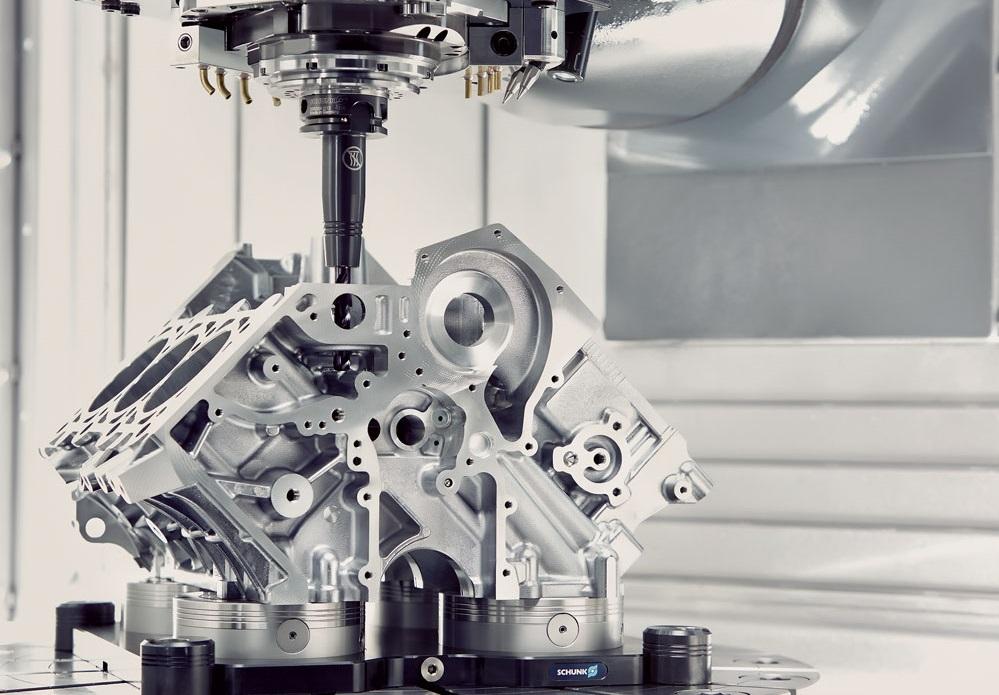
SCHUNK TENDO hydraulic toolholders provide high torque for maximum cutting volume. The larger the toolholder, the more clamping force it can generate. SCHUNK
Many factors and considerations affect toolholder selection. With heavy tools, the machining operation and part features play a significant role in choosing the correct toolholder.
Ensure Machine/Spindle Compatibility
The machine type, features, and spindle size will all determine the best toolholder for the application.
“With larger, heavier tools, one of the things you need to plan for is whether or not the tools can be changed,” said Alan Miller, senior manager, engineering, BIG DAISHOWA Inc., Hoffman Estates, Ill. “The machines have a specific weight limit of tools that they can change, but they also have a moment limit. A moment is a mass at a distance from where the grippers are hanging onto it. So as your tools get heavy and long, they can be underweight and still have too much of a moment that the machine will just drop it.”
When you're working with large and heavy tools, the moment limit is really the first consideration. How can you keep these tools close to a spindle so that you don't exceed the moment limit?
“If it does get beyond that limit, there are some things that can be done with exterior cradles and setups,” said Miller. “For an operator, it's all about considering how to get that heavy angle head or assembly into the machine or how to effectively tool change, whether it's making adjustments where a machine can pick it up or having a procedure to help that operator get that tool into the spindle.”
Another thing to consider is the larger and heavier the tools become, the more room they will take up in the tool magazine.
“Some machinists or operators don’t necessarily realize that putting a toolholder with a heavy tool into a crowded environment in the magazine can cause the magazine to crash,” said Nelu Bilba, manufacturing productivity specialist, ZOLLER Inc., Ann Arbor, Mich. “Knowing the magazine capacity and adjusting to accommodate these larger, heavy assemblies is important.”
If you are unsure about what options are available or which toolholder is best based on machine and spindle specifications, a knowledgeable toolholder manufacturer will help to ensure that all application needs are met and that the toolholder is compatible with the machine tool.
“If you are working with a small spindle size and large or heavy tools, it’s important to choose something with rigidity and vibration-dampening technology,” said Chris Fleurie, national sales manager, clamping group, SCHUNK, Mississauga, Ont. “Something like a SCHUNK TENDO hydraulic toolholder will be a huge benefit in these situations.”
Fleurie noted that these hydraulic toolholders provide high torque for maximum cutting volume. The larger the toolholder, the more clamping force it can generate.
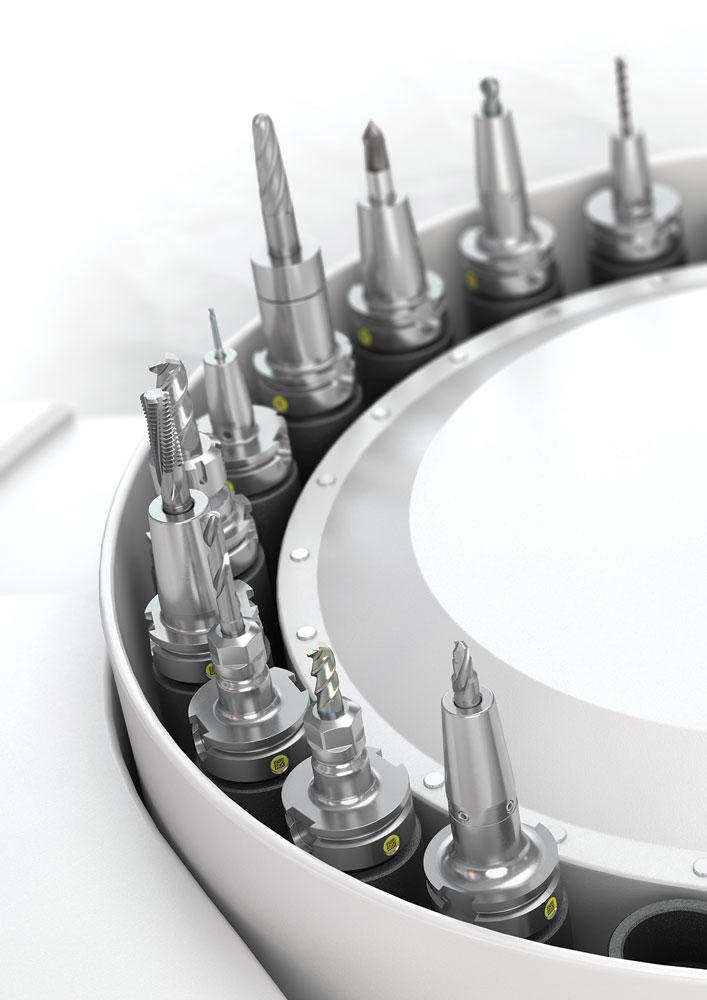
Putting a toolholder with a heavy tool into a crowded magazine can cause the magazine to crash. Knowing the magazine capacity and adjusting to accommodate these larger, heavy assemblies is important. ZOLLER
Balancing the Toolholder and Cutting Tool
Another consideration is prebalancing. Every single tool in the assembly needs to be balanced. The assembly of any toolholder and perishable, whether it's an end mill, face mill, or an insert being changed, needs to be balanced.
“The tiniest of things can throw off the balance,” said Bilba. “But especially with larger, heavy tools, they can introduce lots of vibration during manufacturing, so they must be balanced. There is this misconception that this is only needed at high speeds, but even at a low RPM, the heaviness during the cut will be transferred into the spindle. The integrity of the entire assembly can be compromised.”
Using a face mill as an example, there is a specification on how to torque the inserts into the pocket. For finishing operations, a face mill with an adjustable insert is recommended because you are able to better control the axial runout.
“From an accuracy standpoint, the weak point is the insert, not the machined pocket,” said Bilba. “With a presetter, you can adjust axial and radial runout on a face mill cutter to achieve accuracy in the microns. This will lead to better surface finish and less wear on the spindle. Presetting is essential.”
Having a presetter and setting up these tools off-line is the most effective way to get the best machining results.
“A presetter spindle located right near the end of the machine means that the operator can get the tool in and out of the spindle safely without scratching the presetter cone or the toolholder taper,” said Miller. “This gets that tool close to your body where you can get it directly over the spindle, which is helpful to be able to utilize that type of off-line setup.”
Understand How Features Affect Accuracy and Efficiency
One of the latest updates to toolholding technology is a result of the 2015 revised ASME B5.50 (CAT) standard, which eliminated the reduced section past the V groove, greatly improving radial rigidity for higher-performance milling applications.
This revised standard for toolholders is designed for those big, heavy tools. It allows for a solid connection without weakening the toolholder. However, not all machining centres are capable of accepting the 2015 revision, so use caution before installing these high-rigidity toolholders.
“We don’t see enough people taking advantage of this new standard,” said Miller. “It’s definitely something operators, especially those working with heavy tools, should explore.
“For things like big shell mill holders on 2.5-in. pilots, where these can be 16 in. on a standard old-style CAT holder, it is reduced right down to 2.75 in., right next to where the spindle is,” Miller continued. “But the newer ASME standard allows for upwards of 4 in., making it a lot more rigid.”
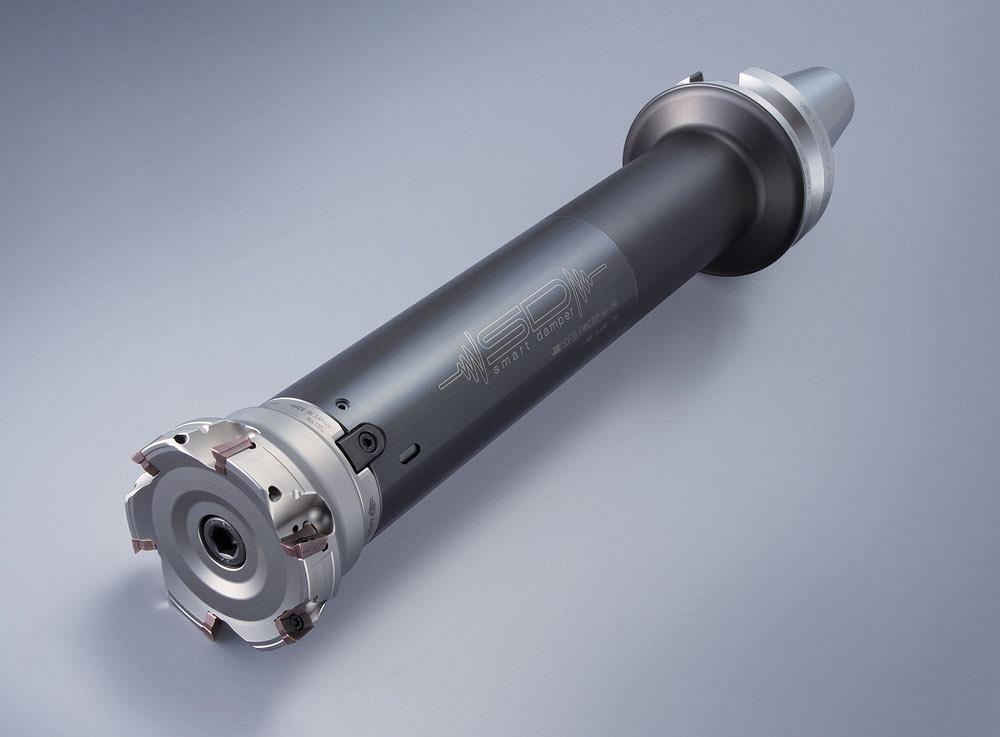
BIG DAISHOWA Smart Damper products can be adapted to create custom tools to extend over 16 in. This enables the damping to be closer to the cutting tool, which helps manage vibration in long-overhang setups. BIG DAISHOWA
Explore How Features Affect Efficiency
Another consideration is toolholder material. Many of the toolholders, especially those manufactured in Europe, have been designed using H-family steel. This material was developed 30 years ago and provides good impact hardness and thermal conductivity.
“Selecting a toolholder that is designed with H-family steel, or something with similar properties, especially for heavy tool applications, is something to consider,” said Bilba. “We did some tests with other steels and the results were catastrophic. It’s important to understand how the toolholder material will affect process reliability.”
Clamping force and vibration dampening also are essential benefits as you get into large milling applications.
“If you look at large end mills, maybe high-feed mills or large drilling applications, clamping force and vibration dampening are some of your biggest factors,” said Fleurie. “Runout and repeat accuracy will have a huge impact on achieving tool life, successful surface finish, and tolerance when machining.”
Coolant-through tools have become increasingly popular. This means that toolholders need to include coolant bores.
“For example, shell mill holders have holes on the front of the face of the holder to allow for coolant to flush through,” said Bilba. “That helps chip evacuation and tool life with a more targeted approach than flood coolant.”
Consider Quick-Change and Custom Systems
Weight is a consideration with larger or even longer tools.
“For example, some large bores are typically long in nature or need longer tools,” said Miller. “That goes back to the weight versus moment limit. Boring tools are all in compression when they're in use, so there's no radial forces on it. That allows for toolholders to have some components to be made using aluminum rather than steel, which cuts down on weight.”
The taper for the machine is still made from steel, but some extensions can be made from aluminum, allowing manufacturers to get longer or larger tool sizes and still be able to tool change. This only applies to tools in compression.
“For face or hollow mills, or similar operations, it’s better to have one single modular holder,” said Bilba. “When you have various components, especially with long reach, you may need various assemblies. This is where a custom toolholder that is designed to a specific length can provide a better solid connection.”
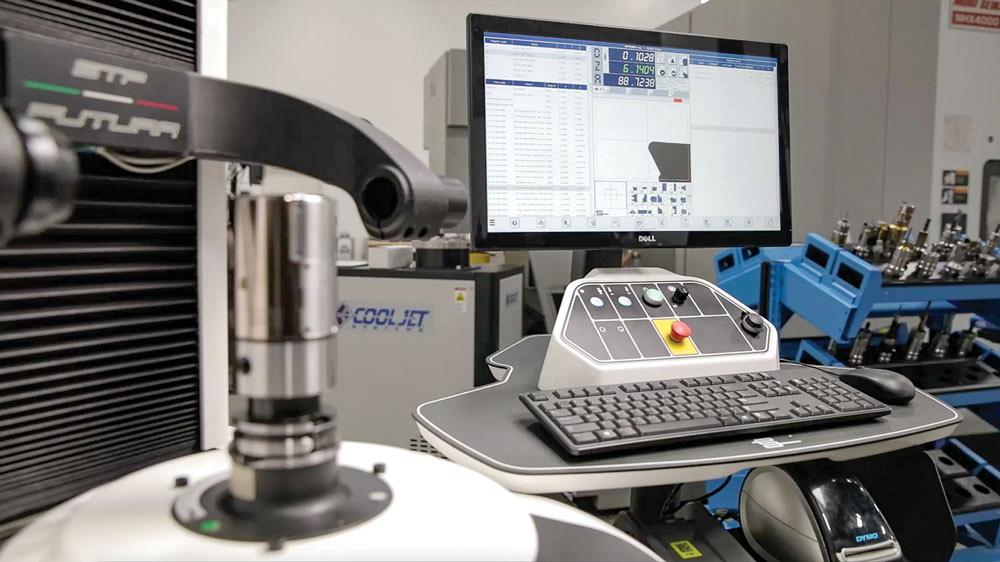
Tool presetters measure the cutting edges of your tools to ensure they precisely match job specifications and are ready to be used in the machine. Adjustments can be completed off-line in less than a minute using a presetter, allowing your machine to continue cutting uninterrupted. BIG DAISHOWA
Associate Editor Lindsay Luminoso can be reached at lluminoso@fmamfg.org.
BIG DAISHOWA Inc., www.bigdaishowa.com
SCHUNK, schunk.com
ZOLLER Inc., myzoller.com
About the Author
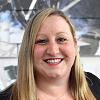
Lindsay Luminoso
1154 Warden Avenue
Toronto, M1R 0A1 Canada
Lindsay Luminoso, associate editor, contributes to both Canadian Metalworking and Canadian Fabricating & Welding. She worked as an associate editor/web editor, at Canadian Metalworking from 2014-2016 and was most recently an associate editor at Design Engineering.
Luminoso has a bachelor of arts from Carleton University, a bachelor of education from Ottawa University, and a graduate certificate in book, magazine, and digital publishing from Centennial College.
subscribe now
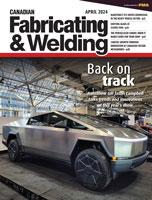
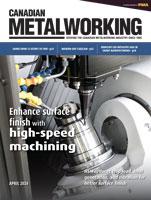
Keep up to date with the latest news, events, and technology for all things metal from our pair of monthly magazines written specifically for Canadian manufacturers!
Start Your Free Subscription- Trending Articles
Automating additive manufacturing
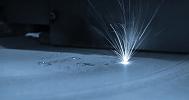
Sustainability Analyzer Tool helps users measure and reduce carbon footprint
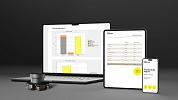
CTMA launches another round of Career-Ready program
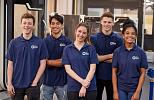
Sandvik Coromant hosts workforce development event empowering young women in manufacturing
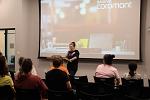
GF Machining Solutions names managing director and head of market region North and Central Americas
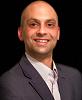
- Industry Events
MME Winnipeg
- April 30, 2024
- Winnipeg, ON Canada
CTMA Economic Uncertainty: Helping You Navigate Windsor Seminar
- April 30, 2024
- Windsor, ON Canada
CTMA Economic Uncertainty: Helping You Navigate Kitchener Seminar
- May 2, 2024
- Kitchener, ON Canada
Automate 2024
- May 6 - 9, 2024
- Chicago, IL
ANCA Open House
- May 7 - 8, 2024
- Wixom, MI