Editor
- FMA
- The Fabricator
- FABTECH
- Canadian Metalworking
Business Profile: GFI
One-stop fabricating and assembly shop focuses on 4 pillars of production for success
- By Rob Colman
- May 1, 2016
- Article
- Fabricating
Pointe-Claire, Que.-based GFI is a great example of a shop that has been able to maintain and grow its business with investments in time- and labour-saving technologies. Established in 1953, GFI is now an operating unit of Thomas & Betts Ltd., a Member of the ABB Group. The company fabricates parts for a variety of OEMs worldwide and specializes in precision and complex metal fabrication of components and assemblies. GFI serves, amongst others, the telecom, aerospace, transportation, and industrial sectors. It serves those customers in every aspect of production, from prototyping to assembly to integration.
The company focuses on four pillars in the production of its products, according to Yves Duchesne, engineering and information systems manager for the company: safety, on-time delivery, quality, and competitive pricing. This focus has helped GFI to create a strong position in the market as one of the largest users of CNC technology for sheet manufacturing in Canada.
When you visit the GFI facility, it is easy to see how this one-stop shop’s approach to process flow assists in the smooth running of the operation. Home to 241 employees, with 62 per cent having at least 10 years of continuous service to the company, the 123,000-sq.-ft. facility houses a various selection of equipment, a growing number of CNC punch/laser machines, and much more. Working with Amada, GFI invests on average $1 million annually in the latest technologies. GFI works with Amada because of the local support it needs for servicing the machines, and the machines meet not only GFI’s productivity needs, but also its health and safety requirements that comprise one of the pillars of its operations.
Duchesne provided Canadian Fabricating & Welding with a tour of the inner workings of the facility, starting with where raw material, including sheets, coils, bars, and extrusions, arrives. GFI works with various grades of aluminum, extruded aluminum, stainless steel, titanium, copper, INCONEL® alloys, and cobalt in its production.
There was a time when GFI did much of its punching on traditional punch presses. Now much of that work is done on its Amada CNC punch presses and punch press/laser combination machines. The company now has six punch/laser combination machines, all bought over the past eight years.
“More and more, this is where we are going [to outfit our facility],” said Duchesne. “We had to replace a CNC punch press, and we replaced it with a combination punch/laser to meet high-mix, low-volume production requirements.” GFI cuts various metals with the CO2 laser, including titanium, aluminum, INCONEL, stainless, and cold-rolled steel.
GFI most recently purchased EML K3610NT punch/laser machines, models that have 56 turret stations, a press capacity of 30 tons, a 4-kW CO2 laser, and a maximum table size of 3,048 by 1,525 mm.
GFI has been working with Amada for the past 30 years and has remained satisfied with its support, which is why Duchesne is interested in making investments in new punch/fiber laser technology in the future.
In addition to the punch/laser technology, GFI has made substantial investments in the latest bending technology, such as five electrical press brakes, all EG 6013 models, over the past two years. GFI made the decision to purchase these machines based on their speed, accuracy, flexibility, and safety. The EG 6013 is a high-speed compact brake with a dual servo power drive system that allows for fast approach, bending and return speeds, which in turn leads to faster cycle times. The controls allow multiple modes of data entry (angle, depth, 2D and 3D). It also has a five-axis back gauge that speeds setup for complex parts.
To complement its CNC cutting and bending technology, GFI continues to invest in other processes such as automated deburring, machining, welding, liquid and powder electrostatic paint lines, 2-D laser marking, and electromechanical testing. and much more. Everything the company does is in the interest of properly serving a very demanding client base.
“We also try to cut waste in everything we do by involving our employees in process improvements in line with the 5S approach and lean manufacturing,” said Duchesne.
With use of newer technologies like the punch/laser combination machine, GFI ensures that there are fewer opportunities for human intervention to affect component parts. It will be interesting to see what the company’s next advance might be.
Editor Robert Colman can be reached at rcolman@canadianfabweld.com
GFI, 514-630-4877, www.gfi.ca
Amada Canada, 450-378-0111, www.amada.ca
About the Author
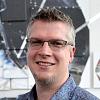
Rob Colman
1154 Warden Avenue
Toronto, M1R 0A1 Canada
905-235-0471
Robert Colman has worked as a writer and editor for more than 25 years, covering the needs of a variety of trades. He has been dedicated to the metalworking industry for the past 13 years, serving as editor for Metalworking Production & Purchasing (MP&P) and, since January 2016, the editor of Canadian Fabricating & Welding. He graduated with a B.A. degree from McGill University and a Master’s degree from UBC.
subscribe now
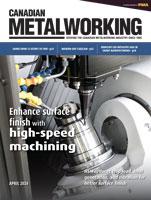
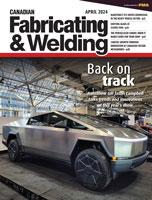
Keep up to date with the latest news, events, and technology for all things metal from our pair of monthly magazines written specifically for Canadian manufacturers!
Start Your Free Subscription- Trending Articles
Aluminum MIG welding wire upgraded with a proprietary and patented surface treatment technology
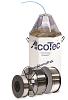
CWB Group launches full-cycle assessment and training program
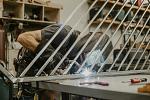
Achieving success with mechanized plasma cutting
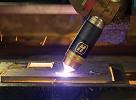
Hypertherm Associates partners with Rapyuta Robotics
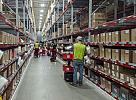
Brushless copper tubing cutter adjusts to ODs up to 2-1/8 in.
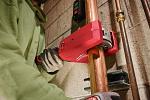
- Industry Events
MME Winnipeg
- April 30, 2024
- Winnipeg, ON Canada
CTMA Economic Uncertainty: Helping You Navigate Windsor Seminar
- April 30, 2024
- Windsor, ON Canada
CTMA Economic Uncertainty: Helping You Navigate Kitchener Seminar
- May 2, 2024
- Kitchener, ON Canada
Automate 2024
- May 6 - 9, 2024
- Chicago, IL
ANCA Open House
- May 7 - 8, 2024
- Wixom, MI