Editor
- FMA
- The Fabricator
- FABTECH
- Canadian Metalworking
Business Profile: Dura-Ramp
Dura-Ramp ups production with plasma, saw, and welding upgrades
- By Rob Colman
- June 1, 2016
- Article
- Fabricating
Chilliwack, B.C.-based Dura-Ramp has been building portable loading docks and loading ramps in the Lower Mainland since the early 1990s. Its ability to create custom builds for clients has helped the company stand out in a niche market. Now, a number of technology upgrades in the shop are creating efficiencies that are making the company that much more competitive.
Like so many businesses, Dura-Ramp grew out of a need that no local business could provide. General Manager Brandon Edwards was working for his father in the early ‘90s in a lumber business when the two were faced with a problem.
“We had a reload facility where we’d bring in materials and then ship them out again to customers across the U.S.,” Edwards recalled. “However, the loading dock was difficult to access directly, so we needed some kind of structure to bridge that gap, and we couldn’t find anything anywhere.”
Edwards commissioned a local fabricator to build this loading ramp system. It worked well for them, although Edwards already felt that he could improve on the design. When their customers in the lumber industry saw what Edwards and his father had come up with, they were keen – it was something many of them needed as well. A new business was quickly born.
But it was the advent of the Internet that really helped the company take off. In 1996 Edwards built the company’s first website. Within two weeks the U.S. military had put in an order.
“That’s when I knew we might have something,” Edwards said.
For 12 years thereafter, Dura-Ramp outsourced production. It wasn’t until the downturn in 2008, when the company’s provider started going through some tough times, that Edwards decided it was time to bring production in-house.
“The downturn was kind of a blessing because it helped us think lean right from the start; we knew we had to keep our costs under control and make everything as efficiently as possible,” said Edwards.
Dura-Ramp rented out a facility for the first five years of business and then, once they felt stable enough, invested in their own 20,000-sq.-ft. facility in Chilliwack.
“We learned from that first five years exactly how our ideal space would be configured, and we were able to make that a reality,” said Edwards. “The ramps and docks we make are quite large. We actually took ideas from truck repair bays we’d seen because the shape of what we make is similar to a trailer. We need plenty of space, and we need to move everything effectively. We also need a lot of yard space for the finished product.”
What Dura-Ramp has created is a series of four bays through which they’ve created a work flow: The raw structural steel and bar grating are cut in the first bay by two separate saws, and from there are welded together with plate that is processed on the shop’s plasma table. Overhead cranes make it easier for the team to properly position products as necessary. The final stop is Dura-Ramp’s paint booth. In all of these departments, the company has made important upgrades in the past few years.
Saw Specialization
Dura-Ramp worked with a fair amount of manual equipment until recently. For instance, to process structural steel, the shop recently switched from a manual saw to a Marvel 380A-PC3-60 vertical automatic CNC band saw machine.
The saw has automatic indexing and a capacity of 15 in. by 20 in. The control has a full-color touchscreen, graphical part programming, and memory for up to 500 jobs and parts stored on removable media. It also includes suggested speed and feed settings for a range of materials, and it stores the settings for each job.
“We needed precise cutoffs from our saw and we weren’t getting it with our old technology,” said Edwards. “With the new technology, we have less rework and faster output. With its automatic feed system we just have to put it in and let the saw do its job.”
Dura-Ramp also invested in a W.F. Wells H-1051-2GRS, a saw designed specifically for cutting bar grating. It has a rectangular capacity of 10 in. high by 51 in. wide, with a 3-degree canted frame.
“It took us a long time to find that saw; it’s very specialized,” said Edwards. “It has a really wide intake space that fits what we make exactly, and it has vises on the top that hold the material down so it doesn’t vibrate. Before we found this we were cutting the grating with a circular saw with a metal-grade blade, cutting one panel at a time. Now we can put seven panels on and cut them all at once.”
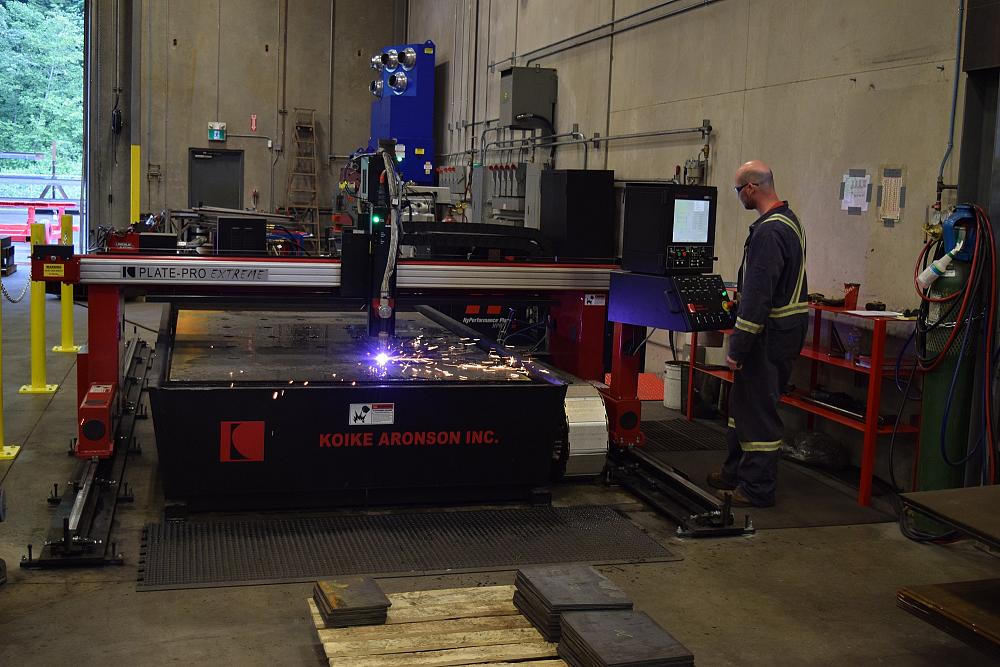
The Koike Aronson table with Hypertherm plasma technology has made plate processing faster and more accurate.
Plasma Upgrade
In the interest of speeding processes, the saws were important, but perhaps biggest recent investment was a new plasma table – a Koike Aronson Plate Pro Extreme CNC plate cutter, purchased via distributor All Fabrication Machinery J.V. (also the company that sold Dura-Ramp its Marvel band saw).
The table uses a Hypertherm high-definition plasma system that includes the Edge II CNC and the company’s HPR260XD® power source, which can produce dross-free cuts in mild steel 1.25 in. thick and has a maximum cutting capacity of 2.5 in. It also includes True Hole® technology, which produces better hole quality than was previously available.
Dura-Ramp’s table is 6 ft. by 12 ft., but its length can be extended should the company wish to add to it in the future. It is set up in the shop now to accommodate that possibility.
“We only installed the plasma table in March but are already seeing great benefits from it,” said Edwards. “The biggest thing that we’re noticing is that when we draw something on our software in the office, it’s exactly what ends up being produced on the table. Before, we were probably cutting certain parts three or four times in some cases to get it right. It is also faster than the table we were using before and can handle thicker materials. And we’re just scratching the surface of what it’s capable of.”
“The other benefit that Dura-Ramp is seeing is that they can save a lot of time on secondary operations,” said Giles Young, sales manager for All Fabrication Machinery. “Often they can just pull the part off the table and it’s ready to go.”
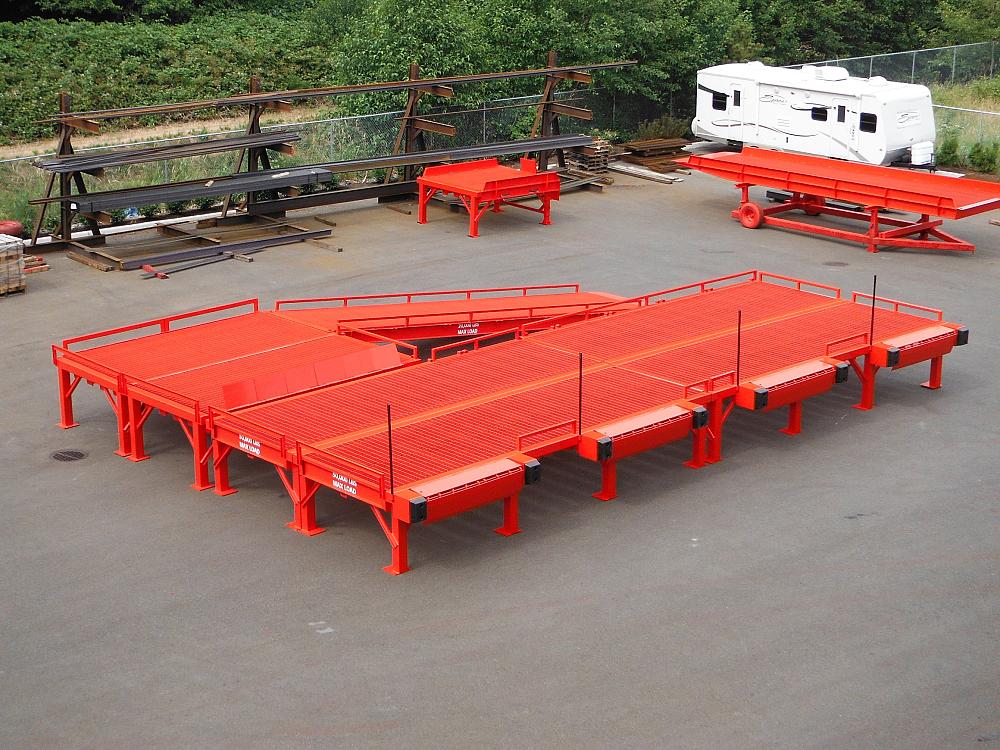
The unit shown here is a custom unit Dura-Ramp designed for a customer that needed to convert a single grade level door into four loading docks. The ramp and first two platforms are located inside the customer’s building. “This is a good example of our quick design-to-delivery time,” said GM Brandon Edwards. “From initial contact, to design, manufacture and delivery we met the customer’s four-week deadline.”
Welding in a Tight Spot
One of the challenges Dura-Ramp has to manage is welding its bar grating to plate, which requires working the weld gun into a very narrow space and trying to keep a steady arc in that space. Edwards found a solution to this at the most recent FABTECH® Chicago event.
“Every time I go to FABTECH I find something that can make us more competitive,” said Edwards. “The Fronius TPS/i welder is something we found last year, and it is phenomenal for what we need to do. We have to get into a 1.5-in. grate. Using this power source, you can be farther away from the material and still get a perfect weld.”
With its Pulse Multi Control (PMC) process, which is part of the TPS/i power source, Fronius provides welders with a tool for improving pulse welding. Two features of PMC are the fusion penetration and arc length stabiliser. The former ensures power remains constant at the weld pool, regardless of whether the stick-out is long or short. The arc length is controlled only with the wire feed speed here, while the arc power at the weld pool remains the same. Along with speed, another advantage is that the fusion penetration remains the same because of the constant power.
The arc length stabiliser is a pulsed arc that creates micro short circuits by assessing and responding to the situation quickly, during which the droplet is transferred into the weld pool. This results in a short, stable arc – readjustment is no longer required. Several different weld seams are covered with just one arc length setting. The characteristic remains unchanged, and readjustment is automatically controlled by the power source.
Paint Efficiencies
Another innovation that Edwards found at FABTECH is a two-component paint system, which mixes the paint immediately prior to being used in the paint booth.
“Most shops mix large amounts of paint at one time and whatever is left over they have to throw out,” Edwards explained. “What this system does is mix it right at the line, producing much less waste.”
Edwards also added a heat system to the paint booth when it was transported from their previous location so that the paint dries much faster.
Since 2012 Dura-Ramp has experienced 20 per cent growth year over year.
With the new saws and plasma table, the Dura-Ramp team can interview their customers about their needs, draw up a custom design quickly, and start processing the job almost immediately. The team of 10 people on the shop floor and three in the office run lean and fast.
With so many innovations in the shop over the past few years, it’s easy to see how Dura-Ramp is staying competitive here in Canada and around the world.
Editor Robert Colman can be reached at rcolman@canadianfabweld.com.
Dura-Ramp Inc., 877-820-1333, www.duraramp.com
All Fabrication Machinery J.V., 855-628-4581, www.allfabmachinery.com
Fronius Canada Ltd., 905-288-2100, www.fronius.ca
Hypertherm, 800-643-0030, www.hypertherm.com
Koike Aronson, 800-252-5232, www.koike.com
Marvel Manufacturing Co., Inc., 800-472-9464, www.marvelsaws.com
W.F. Wells, 269-279-5123, www.wfwells.us
About the Author
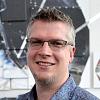
Rob Colman
1154 Warden Avenue
Toronto, M1R 0A1 Canada
905-235-0471
Robert Colman has worked as a writer and editor for more than 25 years, covering the needs of a variety of trades. He has been dedicated to the metalworking industry for the past 13 years, serving as editor for Metalworking Production & Purchasing (MP&P) and, since January 2016, the editor of Canadian Fabricating & Welding. He graduated with a B.A. degree from McGill University and a Master’s degree from UBC.
subscribe now
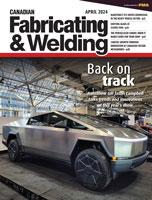
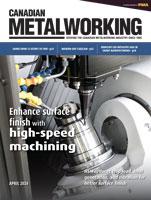
Keep up to date with the latest news, events, and technology for all things metal from our pair of monthly magazines written specifically for Canadian manufacturers!
Start Your Free Subscription- Industry Events
MME Winnipeg
- April 30, 2024
- Winnipeg, ON Canada
CTMA Economic Uncertainty: Helping You Navigate Windsor Seminar
- April 30, 2024
- Windsor, ON Canada
CTMA Economic Uncertainty: Helping You Navigate Kitchener Seminar
- May 2, 2024
- Kitchener, ON Canada
Automate 2024
- May 6 - 9, 2024
- Chicago, IL
ANCA Open House
- May 7 - 8, 2024
- Wixom, MI