- FMA
- The Fabricator
- FABTECH
- Canadian Metalworking
Business Profile: BC Greenhouse Builders
Automating cut-to-length measurement processes increases throughout, and reduces scrap
- By Sue Roberts
- November 1, 2016
- Article
- Automation and Software
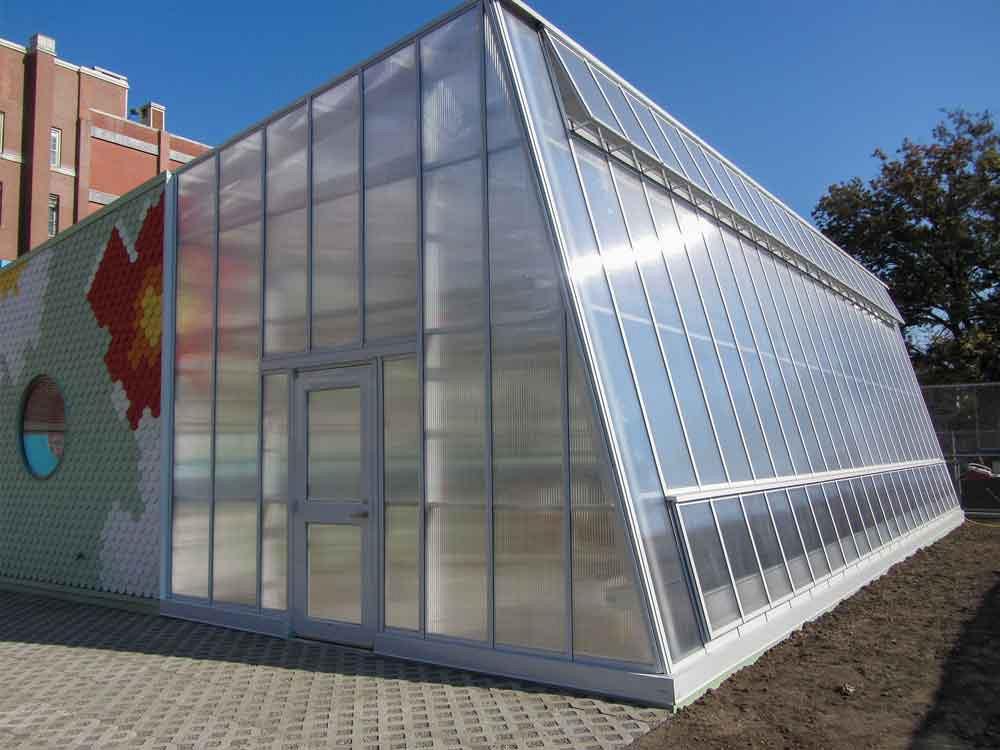
Each BC Greenhouse Builders project is custom-designed, requiring its own set of cut-to-length profiles.
BC Greenhouse Builders in Surrey, B.C., specializes in fulfilling people’s dreams. At least the dreams that involve a luxury greenhouse, conservatory, or garden room. “We understand that having a greenhouse is often someone’s dream,” said Max Tate, production manager. “And the extra effort we put into each project is noticed by the clients.”
Those projects begin with a sales team member working with the customer through the design process. The final result of their collaboration has to live up to the customer’s vision and pass safety and building codes. From there the production team takes over. A CAD drawing is generated for customer approval and then the custom design moves to the shop floor.
Heavy duty, maintenance-free aluminum frames with interior trusses and bracing provide the buildings’ structural support and framework for sheets of glass or polycarbonate. Although no two greenhouses are alike, each structure is built to withstand minimum snow loads of 32 lbs. per square foot and wind gusts up to 85 miles per hour.
Teams of fabricators are dedicated to producing the components that include frames, glazing, long extrusions, doors, and venting. Accurate measurement of each piece is critical to ensuring a precise, secure fit. Each cut length is checked and double-checked prior to shipping to guarantee that there are no surprises when assembly begins on-site.
In many cases, customers are provided with detailed instructions so they can assemble the greenhouses themselves. Tate said, “Our greenhouses are designed so many of our clients can handle installation themselves. However, we have installation teams that fly all over the continent to complete installs for the larger or more intricate projects or to supervise installations by designated contractors.” Structures up to 40 ft. by 100 ft. have been engineered, manufactured, and installed by the company.
Brent Hoogland, production lead hand, said that operators at each aluminum cutting station work from designated cut lists or catalogues of dimensions to cut each part to length. Since each greenhouse is a custom design, the shop has several cut-to-length operations.
The Situation
The manual measure and mark technique used for cutting the aluminum extrusions was too slow to accommodate increasing orders and allowed too much opportunity for inaccuracies. Operators would stretch the tape measure along the profile, mark the cut location with a permanent marker, position the profile, and cut.
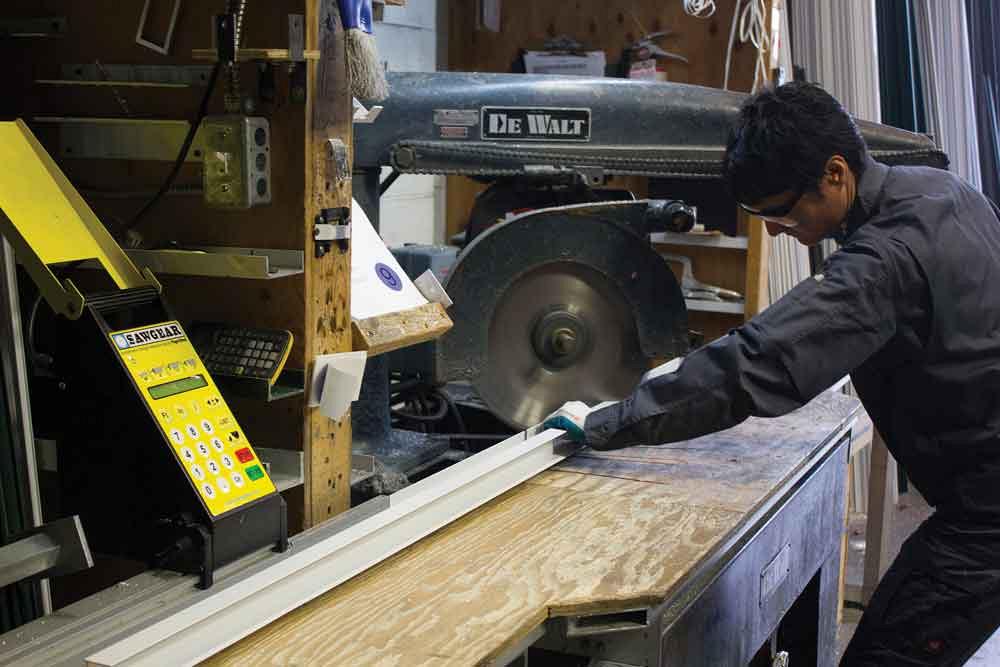
Operator Tyler Higo uses an SG12 system paired with a DeWALT radial arm saw to cut a gable wall piece at a 45-degree angle.
“The chance for a wrong measurement was very high. Someone new, just learning to read a tape measure, could easily mark 45-7/8 in. instead of 45-7/16 in. Or someone could just read a number wrong and cut the aluminum 1 in. short,” said Hoogland.
Those kinds of mistakes, he added, took up production time and could produce expensive scrap with some aluminum profiles costing between $12 and $15 a foot.
The Resolution
Attaching a TigerStop SawGear® automated fence to an existing radial arm saw streamlined the production process and increased throughput. It also made accurate cutting easier, which was apparent in a reduction of waste material.
“After a demonstration model loan and a quick cost-benefit analysis, we opted to purchase a 12-ft. version of the SawGear and install it on our busiest saw. It turns out that the newest piece of technology in the plant is working in conjunction with the oldest—a midcentury DeWALT® radial arm saw,” said Hoogland.
With the automation, a length is are entered into the keypad. The stops move to the proper position for the cut with an accuracy of ±0.008 in., according to the manufacturer. The material is positioned and the cut is made.
“We still work off cut lists, but we’ve eliminated the possibility of measuring the material incorrectly at that station. It contributes to better fittings and quality for our clients,” said Hoogland. “Typing in the measurements instead of measuring and cutting saves us time. We enter the measurement, press start, and cut. The time savings have resulted in increased output.”
Hoogland added that the company has purchased a second 8-ft. SawGear that is paired with a 14-in. radial arm saw that is used for straight cuts in a variety of materials like 1- by 2- by ½-in. angles and 2- by 4- by ¼-in. channel. “This will aid us in achieving our goals of continuous improvement, top-quality product, and increased profitability.”
Associate Editor Sue Roberts can be reached at sroberts@canadianfabweld.com.
Photos courtesy of BC Greenhouse Builders Ltd., 888-391-4433, www.bcgreenhouses.com
TigerStop, 360-254-0661, www.tigerstop.com
About the Author
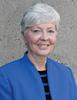
Sue Roberts
2135 Point Blvd
Elgin, IL 60123
815-227-8241
Sue Roberts, associate editor, contributes to both Canadian Metalworking and Canadian Fabricating & Welding. A metalworking industry veteran, she has contributed to marketing communications efforts and written B2B articles for the metal forming and fabricating, agriculture, food, financial, and regional tourism industries.
Roberts is a Northern Illinois University journalism graduate.
subscribe now
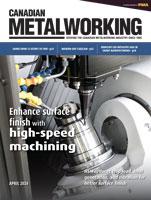
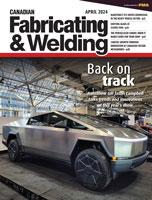
Keep up to date with the latest news, events, and technology for all things metal from our pair of monthly magazines written specifically for Canadian manufacturers!
Start Your Free Subscription- Trending Articles
Aluminum MIG welding wire upgraded with a proprietary and patented surface treatment technology
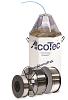
CWB Group launches full-cycle assessment and training program
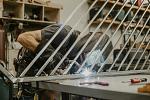
Achieving success with mechanized plasma cutting
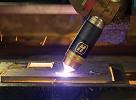
Hypertherm Associates partners with Rapyuta Robotics
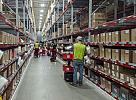
Brushless copper tubing cutter adjusts to ODs up to 2-1/8 in.
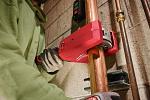
- Industry Events
MME Winnipeg
- April 30, 2024
- Winnipeg, ON Canada
CTMA Economic Uncertainty: Helping You Navigate Windsor Seminar
- April 30, 2024
- Windsor, ON Canada
CTMA Economic Uncertainty: Helping You Navigate Kitchener Seminar
- May 2, 2024
- Kitchener, ON Canada
Automate 2024
- May 6 - 9, 2024
- Chicago, IL
ANCA Open House
- May 7 - 8, 2024
- Wixom, MI