Editor
- FMA
- The Fabricator
- FABTECH
- Canadian Metalworking
Welding Tech: Welding aluminum - Cleanliness is key
Gas tungsten arc welding is the ideal process for aluminum welding, but doing it right takes time
- By Rob Colman
- UPDATED February 13, 2023
- July 12, 2016
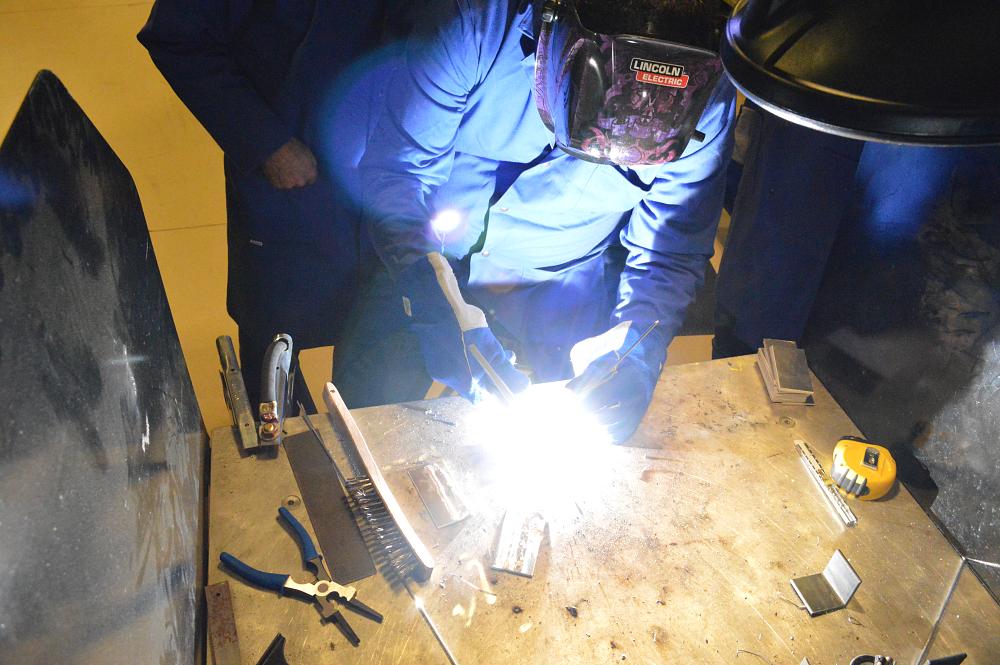
Canadian Fabricating & Welding sat down with Ken Thorn, global welding engineer at the Canadian Welding Bureau, to learn more about what a welder should be attentive to when working with aluminum.
For welding aluminum parts, gas tungsten arc welding (GTAW) is the ideal process. The control the welder has leads to high-quality welds.
Canadian Fabricating & Welding sat down with Ken Thorn, global welding engineer at the Canadian Welding Bureau, to learn more about what a welder should be attentive to when working with aluminum.
“GTAW really is the Cadillac of welding processes,” Thorn said. “It puts the control of the whole welding process in your hands. You’ve got control of the heat input. The torch is in your hand, and in most GTAW systems you’ve got some way to remotely control the current — either a foot pedal or a thumb wheel on the torch — so you can adjust the current as you go. This way, if you are welding and can see the weld pool is about to melt through, then you can reduce the current, and if the weld pool is shrinking you can increase the current on-the-fly. The filler metal is added separately from the arc, and you have complete control over when to add it to the weld pool and how much to add. In the hands of a skilled welder, it is a very high-quality process.”
Cleanliness is Critical When Welding Aluminum
Like so many welding processes, cleanliness is critical.
“Aluminum is very sensitive to contamination on its surface,” said Thorn. “If you have a contaminated surface, you’ll run to porosity in the weld metal.
“Aluminum also has a thin layer of aluminum oxide on its surface, and you need to deal with that layer to get proper penetration and fusion into the joint.”
The aluminum oxide layer is uneven, and wire brushing is too insubstantial to clean the weld area properly. It requires a cathodic cleaning.
“Essentially, you weld the joint twice,” said Thorn. “Aluminum oxide has a high melting temperature, which means you have to use alternating current when you weld aluminum. The electrode-positive half of the waveform produces a cleaning action on the parent metal, and the electrode-negative half of the form heats it. The former breaks up the oxide layer and cleans it off, and the latter heats the base metal and melts it.”
Thorn noted that how you manage the cleaning and heating balance will depend on what kind of equipment your shop has.
“Older equipment, transformer-based power sources, have their place but are less flexible in welding aluminum compared to newer inverter-based power sources,” Thorn explained. “If you’ve got an older conventional machine, you set the AC balance control to the ‘clean’ setting, which changes the shape of the voltage waveform towards the electrode to positive mode and uses a low current to pass along the joint and clean it. Moving along the joint with the low current does not melt the parent metal, it just breaks up the oxide layer. You can see it breaking up the oxide layer and producing a sort of frosty appearance on the surface of the aluminum.”
Once the joint is cleaned, you readjust your AC balance to the “weld”, “penetration” or “fusion” setting (each power source builder uses a different term), increase the current, and make the weld. In the “weld” setting, the shape of the waveform is changed to increase the time in the electrode-negative mode. Figure 1 shows typical voltage wave forms for three settings of an AC balance control on a power source.
Thorn noted that with the inverter—based power source you do basically the same thing, but this type of power source allows greater control of the waveform.
“The range of variation of the shape of the waveform between electrode-positive and electrode-negative is increased in inverter-based power sources. You can set the power source to 90 per cent electrode-positive, which gives you a better cleaning action. Inverters also allow you to adjust the frequency of the AC to give you a better focus on the arc and, during the weld, better penetration. Increasing the alternating frequency of the waveform to values greater than 60 cycles per second focuses the arc. Some people might describe this as a ‘stiffer’ arc.”
The only sticking point among welders who use inverter-based power sources is the distinct and very loud sound that they make.
The challenge with using transformer-based power sources for aluminum GTAW ith that they require a high-frequency generator in them, and it has to be in a continuous mode.
“If you are welding steel, the difficulty when trying to strike an arc is that you have to electrically jump the gap between the tip of the electrode and your workpiece to start the arc,” Thorn explained. “One way to do this is to put a high—frequency spark across it that will ionize the shielding gas and start the arc. In steel welding the high-frequency arc start buzzes for half a second, the arc is started, and then the high-frequency current is turned off.
“When welding aluminum you need to have continuous high frequency because with AC the arc goes to zero voltage every half-cycle, and you need to re-establish the arc every time it does. Basically the arc will go out, and if it isn’t restarted, that is almost like rectifying it. Effectively you go from AC to DC, but you are getting only half of the wave. The continuous high frequency is needed to restart the arc every half-cycle. The high frequency runs only at 5 milliamps, a very low background current, but it needs to be there.”
In terms of electrodes used in the process, Thorn noted it’s always “green for clean” — meaning you use a pure tungsten electrode (colour-coded green on its end) to clean the surface. It is possible to use pure tungsten electrodes because the current used to clean the parent metal is low and they do not overheat. Once the cleaning has been completed, the tungsten electrode is changed to one designed for welding.
“In GTAW the electrode doesn’t get melted, which is why you use tungsten; it has a high melting point,” Thorn explained. It is not particularly efficient in emitting electrons to make a welding arc and it tends to overheat, so for welding, a small amount of cerium, lanthanum, or thorium is added to the tungsten to make it easier for the electrode to emit electrons.”
Ceriated or lanthanated electrodes tend to be chosen over thoriated electrodes now because of the slight radioactivity in the latter.
Welding Aluminum Takes Patience and Practice
Thorn stressed that to get a good aluminum weld requires patience and practice.
“Shops that typically weld steel will get a little contract for an aluminum cap on a trailer or something and will think, ‘We’ve got a lot of skilled welders so they’ll be able to take care of this no problem.’ But aluminum is different. It behaves differently. It doesn’t change colour before it melts, and you have to weld it hot and fast. Without some training and practice, you can get into trouble in a big hurry.”
Editor Robert Colman can be reached at rcolman@canadianfabweld.com.
Canadian Welding Group, 800—844—6790, www.cwbgroup.org.
subscribe now
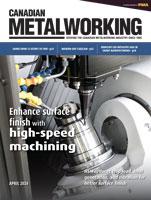
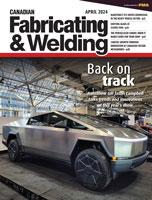
Keep up to date with the latest news, events, and technology for all things metal from our pair of monthly magazines written specifically for Canadian manufacturers!
Start Your Free SubscriptionAbout the Author
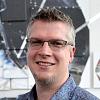
Rob Colman
1154 Warden Avenue
Toronto, M1R 0A1 Canada
905-235-0471
Robert Colman has worked as a writer and editor for more than 25 years, covering the needs of a variety of trades. He has been dedicated to the metalworking industry for the past 13 years, serving as editor for Metalworking Production & Purchasing (MP&P) and, since January 2016, the editor of Canadian Fabricating & Welding. He graduated with a B.A. degree from McGill University and a Master’s degree from UBC.
- Trending Articles
Aluminum MIG welding wire upgraded with a proprietary and patented surface treatment technology
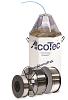
CWB Group launches full-cycle assessment and training program
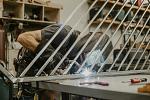
Achieving success with mechanized plasma cutting
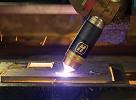
Hypertherm Associates partners with Rapyuta Robotics
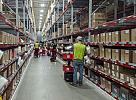
Brushless copper tubing cutter adjusts to ODs up to 2-1/8 in.
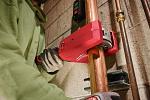
- Industry Events
MME Winnipeg
- April 30, 2024
- Winnipeg, ON Canada
CTMA Economic Uncertainty: Helping You Navigate Windsor Seminar
- April 30, 2024
- Windsor, ON Canada
CTMA Economic Uncertainty: Helping You Navigate Kitchener Seminar
- May 2, 2024
- Kitchener, ON Canada
Automate 2024
- May 6 - 9, 2024
- Chicago, IL
ANCA Open House
- May 7 - 8, 2024
- Wixom, MI