- FMA
- The Fabricator
- FABTECH
- Canadian Metalworking
Welding Tech: Consider all factors in welding throughput improvements
New technologies make it possible to increase weld speeds, but prep work and consumables also play a role
- By Nestor Gula
- May 11, 2016
Increasing welding throughput is the goal of every welding shop. It’s true that you can weld only so many inches per minute, but good preparation practices, the right consumables, and modern welding power sources can all help speed up the process.
One way to increase throughput with gas metal arc welding (GMAW) is to move from a conventional GMAW to a pulse GMAW process. A power source that uses a pulse process has several ways to increase welding speed.
“One way we do so is to modify the arc so that the weld puddle is less fluid, which allows the welder to move faster,” said Justin Durik a welding engineer for Miller Electric Mfg. Co.
Lincoln Electric has introduced a variation on the pulse mode with a technology it calls Rapid X™. It uses a very short arc length for speed. But in addition it has a low-current “wet-in” technology that momentarily drops the current at the moment the molten droplet contacts the weld puddle. This reduces spatter after the droplet detaches.
“Rapid X can increase travel speed up to 40 per cent over more traditional pulse modes,” said Scott Stanley, national marketing manager for the Lincoln Electric Company of Canada. “It does so by using an extremely short arc length that remains stable at high speeds.”
However, switching to a pulse GMAW process won’t work for every application.
“There are too many variables in the parameters,” said Dave Almy, a welding engineer with Miller Electric Mfg. Co. “Changing parameters is going to change the penetration pattern. Increasing travel speed will change the penetration pattern. So when we get into these types of questions with end users, we ask, ‘What is the requirement?’” Almy encourages welders to understand the material they are working with and the speed they hope to achieve and work back from there to establish the fastest solution for that particular application.
For shops with older machines, increasing welding speed might require investing in new equipment. However, there are some methods that can increase speed slightly without negatively affecting quality or requiring new equipment.
“For conventional GMAW, if you are running a constant-voltage (CV) process at a given voltage [keeping the welding arc constant] to go faster, I would just increase the wire feed speed,” Almy said.
General rules to increase productivity are difficult to apply because welding throughput depends on the application, base material, thickness, and joint preparation.
“Sometimes, like in thick plate butt welding, the deposition rate of the welding process drives overall welding productivity,” said Ed Hansen, global director of product management, flexible automation for ESAB. “In this case, more wire mass per unit of time means more work done and higher productivity. Here we have options to choose wire sizes, wire chemistries, and multiple-wire setups that can dramatically increase productivity. It is not uncommon to increase productivity by three to four times just through adjusting wire size and shifting to a twin or tandem process. Often, the limiting factor in these applications becomes heat input limitations needed to achieve suitable mechanical properties in the weld.
“In other cases, like thin plate fillet welding, pure welding travel speed drives overall productivity. Users have a choice of welding processes that can make the first level of improvement in welding travel speeds. High arc stability and an efficient wire transfer process are required for achieving high speeds. Then the user has options for choosing welding wires that perform better at high speeds.”
Preweld Work
Welders will not increase their weld throughput by implementing preweld shortcuts.
“Basically, if everything is prepared correctly and clean, you won’t have to go back and clean things,” said Valarie Wojcik, a welding engineer for Miller Electric Mfg. Co. “[Without a clean surface] you can have lack of fusion, entrapment, porosity, cold lap – sometimes inclusion depending on what kind of material it is.” With good parts setup and proper preweld preparation, welding throughput will be good and not suffer quality issues.
“Any contaminants on your material will change the bead and will potentially make the operator slow down, which means lower throughput,” said Almy.
Different processes call for specific preweld procedures.
“To get the best productivity out of submerged arc welding (SAW), the goal is to avoid manual root runs and to be able to start welding directly with the SAW process,” said Hansen. “Because the SAW process requires a zero gap to avoid burn-through, the accuracy of the bevel concerning root face, straightness, and angle is extremely important. The typical methods for bevel preparation are cutting or milling.”
“When a company takes careful steps before welding, such as implementing proper cleaning, it reduces the chance of having to rework a part due to quality issues,” said Caleb Haven, a welding engineer at Hobart Brothers Company. “Activities such as proper preheat also minimize the risk of crack sensitivity, so there is less necessity for rework. Essentially, good preweld preparation helps ensure companies get the job done right the first time.
“It is also important to have a clean base material. Some wires, like metal-cored wire, are more tolerant of contaminants on base materials and can weld through them, so these applications may require less or no precleaning. Metal-cored wire can typically weld through dirtier material better than solid wires and produces less spatter. Those features can help eliminate preweld activities like grinding or applying antispatter.”
Wire Strategies
Selecting the proper wire can further increase welding efficiency.
“For flux-cored and metal-cored wires, designing with a higher level of fill (larger core-to-sheath ratio) will increase the amount of metal deposited per ampere of current used. This allows deposition rates to be increased without increasing heat input,” said Dave Meyer, technical liaison at ESAB. Simple choices like using wires designed to minimize spatter “can significantly improve throughput by reducing postweld cleanup. Of course, spatter reduction is also dependent on the use of the proper shielding gas and proper welding procedure,” he said. “Use of wire in bulk packaging reduces downtime required to change from one spool to the next.”
Larger-diameter wires can provide better deposition rates to complete the weld faster “and can be especially helpful in improving throughput in operations with a wide range of applications with varying material thicknesses or joint type,” said Haven. “The actual deposition rate that a wire provides will depend on the specific diameter and type of wire, for example, metal-cored, flux-cored, or solid wire. To a large degree, the ability of a wire to speed up welding is based on the application and joint design, as well as the material being welded. For example, there are metal-cored wires available for welding coated or galvanized steels. These wires offer faster travel speeds compared to solid wires, as well as less subsurface porosity. These wires increase efficiencies by getting the job done quicker, with fewer quality issues, so that time can be spent producing more parts instead of focusing on rework.”
Automated Systems
Some arc welding process modes lend themselves to higher deposition or higher travel speeds, in which case automation becomes the ideal option.
“For instance, in GMAW, high-speed rotational arc welding processes like ESAB’s Swift Arc Transfer (SAT™) can achieve travel speeds that are double that of conventional spray or pulse welding while maintaining good penetration,” said ESAB’s Hansen. Using non-copper-coated wires, SAT produces flat welds suited for fillet and overlap welds in thin to thick plate, in downhand positions.
“For higher productivity, there are processes like hybrid laser arc welding (HLAW), which can achieve travel speeds five to 10 times higher than conventional arc welding and can at the same time penetrate deeply enough to replace as many as five passes of a conventional arc weld,” Hansen noted.
Nestor Gula is a Toronto, Ont.-based freelance writer. He can be reached at nestor.gula@yahoo.ca.
ESAB Welding & Cutting Products, 877-935-3226, www.esab.ca
Hobart Brothers Co. 888-489-9353, www.hobartbrothers.com
Lincoln Electric Canada, 416-421-2600, www.lincolnelectric.ca
Miller Welding Automation, 920-734-9821, www.millerwelds.com
subscribe now
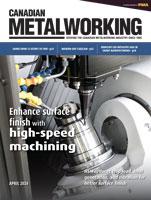
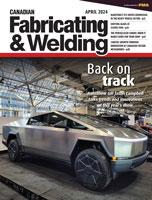
Keep up to date with the latest news, events, and technology for all things metal from our pair of monthly magazines written specifically for Canadian manufacturers!
Start Your Free SubscriptionAbout the Author
- Trending Articles
Aluminum MIG welding wire upgraded with a proprietary and patented surface treatment technology
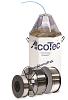
CWB Group launches full-cycle assessment and training program
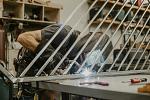
Achieving success with mechanized plasma cutting
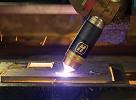
Hypertherm Associates partners with Rapyuta Robotics
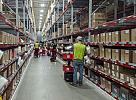
Brushless copper tubing cutter adjusts to ODs up to 2-1/8 in.
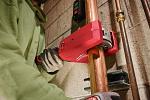
- Industry Events
MME Winnipeg
- April 30, 2024
- Winnipeg, ON Canada
CTMA Economic Uncertainty: Helping You Navigate Windsor Seminar
- April 30, 2024
- Windsor, ON Canada
CTMA Economic Uncertainty: Helping You Navigate Kitchener Seminar
- May 2, 2024
- Kitchener, ON Canada
Automate 2024
- May 6 - 9, 2024
- Chicago, IL
ANCA Open House
- May 7 - 8, 2024
- Wixom, MI